The process of coating the surface of products with metal or special alloys (mostly shiny) in thin layers to enhance their beauty and strengthen them against corrosion, oxidation, or impact is referred to as plating.
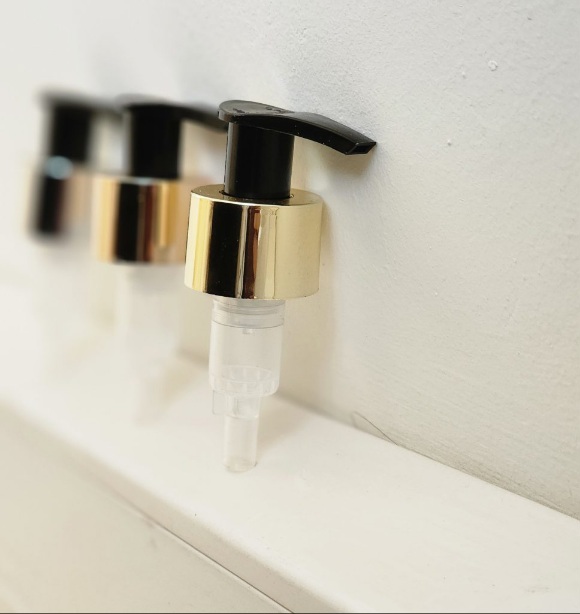
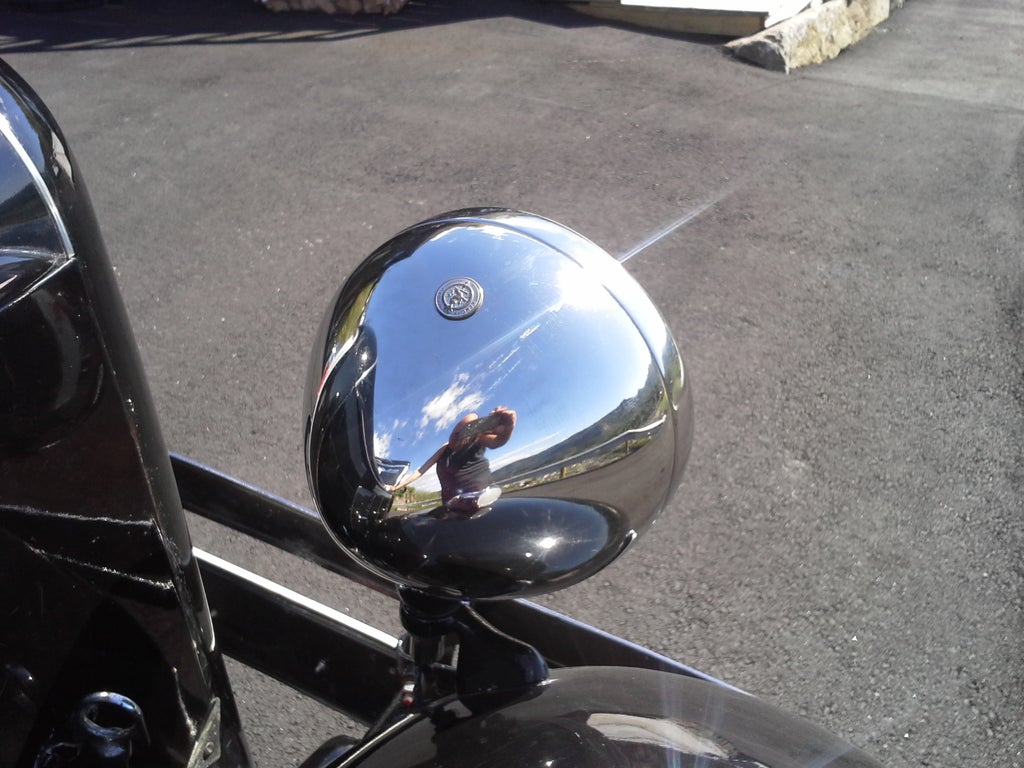
-Plating HistoryThe plating industry first emerged in the 1960s when the American automotive industry began using it to improve the quality of painted products. However, due to limited facilities at that time, the process was challenging and faced multiple obstacles, causing the industry to be forgotten for a while.
The increasing weight of cars at that time led to greater reliance on fossil fuels, resulting in numerous expenses and pollution. As a result, European car manufacturers started considering the production of lighter vehicles, which ultimately led to the use of plastic components.
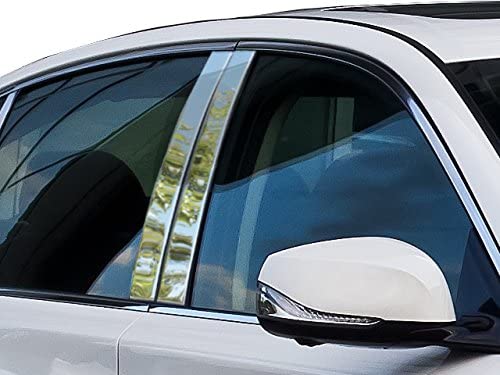
However, this process is much more difficult than it appears.

–Vacuum plating, also known as vacuum metallizing, is a plating method where the thickness of the plated layer is extremely thin. However, the layer completely covers the surface of the product, and its color remains resistant to severe and constant impacts.
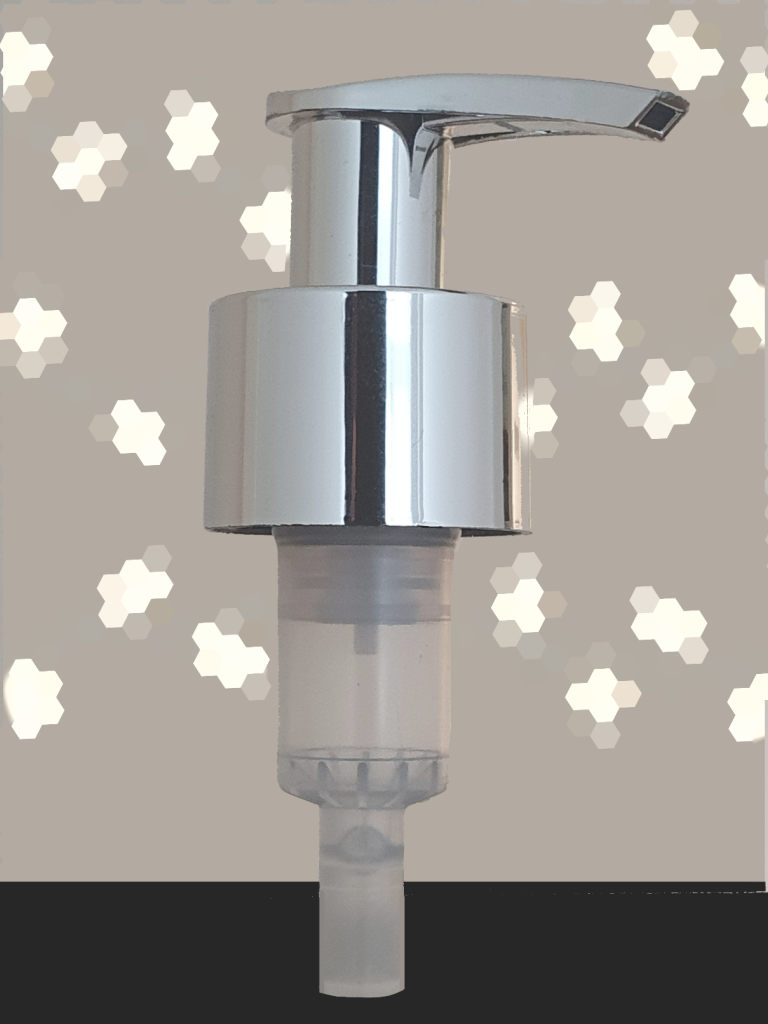
–And the last method is laser plating
This method is predominantly used for plastic and polymer products and is considered a modern technique. It is employed to enhance the shine and beauty of the products.Among other plating methods, laser plating is relatively more expensive.
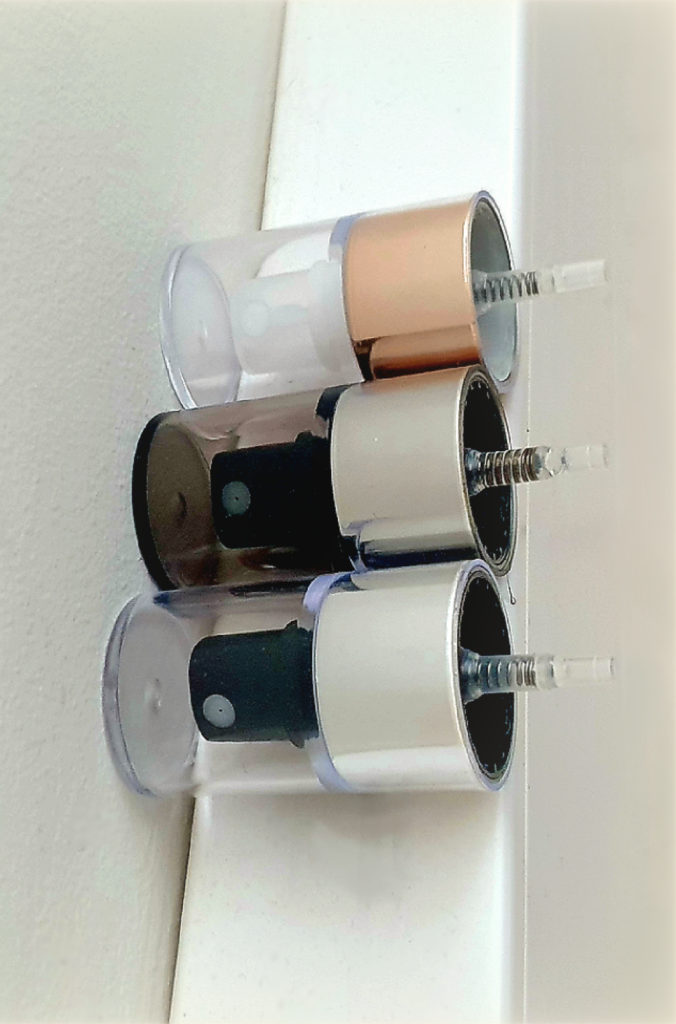